Henry Ford: el empresario al que se le ocurrió la producción en serie o masiva después de visitar un rastro
La línea de montaje en movimiento cambió la forma en que se fabrican los automóviles.
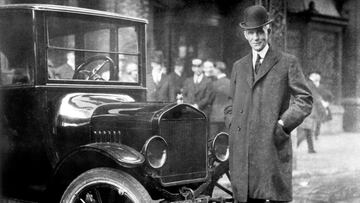
Si bien Henry Ford no fue el inventor del automóvil, si logró que este medio de transporte revolucionara la movilidad de las personas en el todo el mundo, gracias a que logró reducir el precio a lograr una producción masiva.
Esta capacidad de producción en masa fue gracias a que el fundador de Ford Motor Company implementó, en 1913, la producción en serie del Model T por medio de líneas de montaje.
Debido no se producía unidad por unidad, esta modalidad de fabricación, no solo se logró reducir los costos,sino también porque permitió hacer más rápida y grande la producción de automoviles.
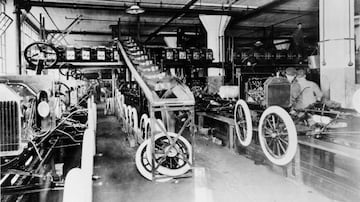
Para tener una idea del impacto que de la producción masiva en el precio es que antes su introducción el Model T costaba 835 dólares, mientras que después de su implementación el costo era de 260 dólares.
Algo grandioso de este método de producción en línea o en serie, es que además de revolucionar la manufactura del automóvil, hizo que otras industrias replicaran el procedimiento en sus respectivas fábricas.
Por increíble que parezca, la idea de Henry Ford de implementar la línea de montaje en la fabricación de automoviles, provino del matadero Swift & Company, ubicado en Chicago, Illinois.
Tras visitar este rastro, y observar que los cerdos muertos eran colgados para queser destazados hasta obtener todas las piezas carne, Henry Ford pensó que sería una buena idea replicar esa línea de desmontaje, solo que, a la inversa, en la producción del Model T.
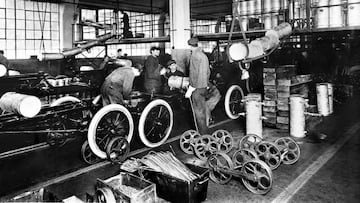
No obstante que Henry Ford adoptó esta técnica del rastro a los automóviles, la perfeccionó dándole movimiento por medio de cintas transportadoras. Esto permitió que la labor de ensamble de una pieza en específico, se llevara a los trabajadores en lugar de que el trabajador se moviera hacia y alrededor del vehículo.
Con esta innovación, el vehículo era arrastrado por la línea y construido paso a paso. Al principio fue tirado por una cuerda, y luego se convirtió en un simple mecanismo de cadena móvil. Así, en lugar de pasar horas y horas en la producción de un solo vehículo, fue posible ensamblarlo en solo 90 minutos.
A pesar simplificar la producción, curiosamente, la mayoría de los trabajadores Ford Motor Company renunciaron para irse a trabajar con la competencia, debido a que se aburrían en la línea de montaje. En lugar de trabajar para construir un vehículo completo, solo hacían una o dos tareas.
Además, a los trabajadores no les gustó que se les exigiera un tiempo en específico para su labor, esto debido a que la línea de montaje estaba en movimiento. Esta situación hacía que a ciertas unidades les faltaran piezas o que algunos trabajadores cayeran unos sobre otros mientras armaban el automóvil.
Para convencer a los trabajadores de que se no renunciaran, Henry Ford introdujo la jornada laboral de cinco dólares por jornada, el doble del sueldo diario por trabajador. Esta estrategia que cientos de personas de todo Estados Unidos migraran a Detroit en busca de ser contratados por Ford.
Trabajar en Ford no solo significaba tener un sueldo superior, sino era trabajar menos por más, ya que también redujo la cantidad de horas laborales.